
ENVIRONMENTAL
Protecting the environment and efficient use of resources are core elements of our sustainability strategy.
We pay attention to
the climate and resources
In line with this, we focus on climate protection, work on active waste management and pay attention to the sensitive use of water.
CLIMATE CHANGE
CLIMATE CHANGE
The importance of climate change for BENTELER became evident in our materiality assessment. As a result, we address energy-efficient use, climate protection, and the consequences of climate change.

Efficient use of energy
Efficient use of energy
Our focus is clear: We want to increase our energy efficiency and the share of energy from renewable sources. Therefore, many projects were implemented to reduce our consumption.
Also, our procurement focusses on the purchase of renewable energy: Through intensified activities and measures, we already cover more than 50 % of our electricity consumption with renewable energy sources. This is a significant increase compared to the previous year (2023: 47,4 %).
This share will be increased in the future by concluding PPAs, generating our own electricity and purchasing guarantees of origin.

Climate protection: Reducing emissions in production
Climate protection: Reducing emissions in production
BENTELER aims to have net-zero emissions by 2050. Along the way, our goal is to reduce production-related absolute Scope 1 and 2 GHG emissions by 50% by 2030 compared with the 2019 baseline. By 2040, we aim to avoid or offset 100% of the absolute GHG emissions in our production.
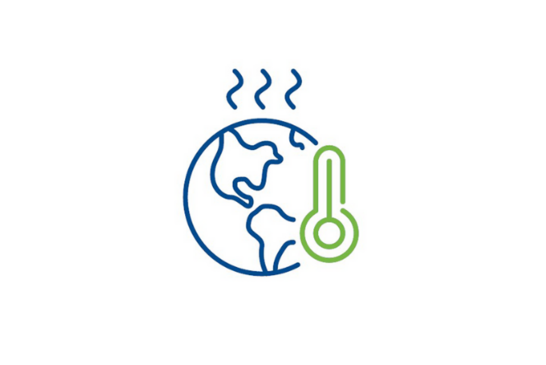
BENTELER's CO2 emissions
We are currently well on the way to achieving our climate change mitigation targets. BENTELER Groupʼs Scope 1 and 2 emissions fell to 482,951 t CO2e in 2024. This represents a 26% reduction compared to the previous year and 42% compared to 2019. This is due in particular to the increased use of electricity from renewable energies.
To further reduce our emissions, we are focusing on substituting fossil fuels in our internal production processes (Scope 1). We are therefore looking into alternative renewable energies such as green hydrogen or green electricity in order to use them for energy-intensive heating processes in our production. A pilot project at our Paderborn plant Talle, Germany, is replacing gas burners in a hot-forming furnace with electric heating elements in order to save up to 150 tons of CO2 per year.
Reduction of Scope 2 emissions
The key to reducing our scope 2 emissions is PPAs, which should cover the majority of our electricity requirements by 2030. Where possible, we will also connect renewable energy sources directly to our plants via onsite PPAs. Depending on local conditions, we will also generate emission-free electricity on our plant sites themselves. For example, photovoltaic systems have already been installed at the Shenyang, Vigo, Mos and Schloss Neuhaus sites. The planned PPAs and self-generation will enable us to secure our long-term electricity supply. The first PPAs have already been concluded. This approach will be expanded further in the future.
The electricity portfolio is supplemented by purchased green electricity (green electricity contracts or upgrades to existing conventional electricity contracts with certificates of origin) in order to be able to flexibly cover fluctuating energy requirements.
Emissions in the supply chain (Scope 3 emissions)
We are also continuing to drive forward the optimization of our carbon footprint in our supply chain. By the end of 2030, we aim to reduce our upstream absolute Scope 3 GHG emissions here by 30% (compared to 2019). To achieve this goal, it is first necessary to increase the transparency of emissions, especially from the supply chain upstream of BENTELER.
Common goals in the supply chain
In 2022 and 2023, the BENTELER Group informed over 5,000 suppliers about the CO2 reduction targets that BENTELER has set itself in the supply chain. In addition, the largest suppliers (80% of the direct purchasing volume) were recruited to support these targets. The dialog on target achievement is currently being continued. At the same time, the largest suppliers (80% of the purchasing volume) across all divisions were surveyed about their own CO2 targets and asked for their opinion on the BENTELER targets. The survey was combined with a request to submit a voluntary commitment to our targets.
Partnering for climate protection
Partnering for climate protection
In the steel sector, we have issued various declarations of intent to purchase green steel, for example with ArcelorMittal Europe and POSCO. BENTELER Automotive and thyssenkrupp Steel Europe are also joining forces on climate protection. BENTELER has secured climate-friendly bluemint® Steel from thyssenkrupp for the long-term production of vehicle components. bluemint® Steel has a significantly reduced level of CO2. The cooperation between the two companies will be further intensified from 2026. The steel will then come from direct reduction plants in conjunction with meltdown units, which will be operated with green hydrogen and green electricity.
Green steel from BENTELER's own steel mill in Lingen is also playing an increasingly important role. With 75% fewer emissions in production than conventional blast furnace steel, we can thus offer our customers products produced in a climate-friendly way. Test projects are underway and various approaches are being clarified regarding the technical feasibility, extent, and way production can be increased.
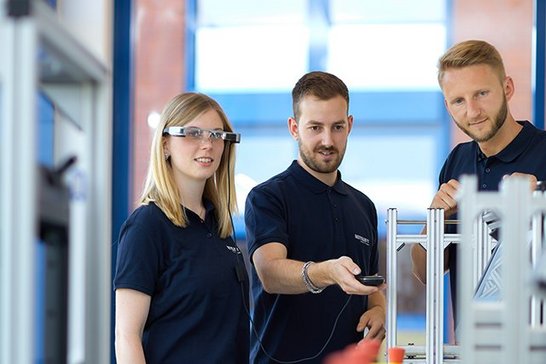
Success in climate ratings
Success in climate ratings
The success of our activities to optimize emissions is also reflected in the CDP (Carbon Disclosure Project) rating. In 2024, the BENTELER Group achieved a B rating in the Climate Change and Water categories.
The CDP is a non-profit organization that operates the global disclosure system for investors, companies, cities, states, and regions to manage their environmental impact. It has the largest environmental database in the world. CDP's findings are widely used to inform investment and procurement decisions towards a zero-carbon, sustainable and resilient economy.
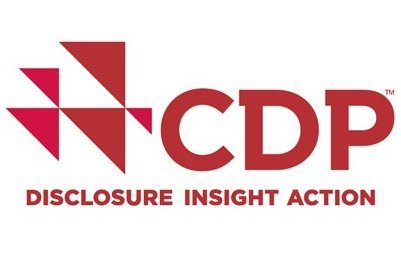
Bronze in the EcoVadis rating
Bronze in the EcoVadis rating
With “Bronze” in the EcoVadis rating, BENTELER is among the top 35% of the companies assessed. EcoVadis is one of the world's largest providers of sustainability ratings. Sustainability management was validated and evaluated in relation to the areas of environment, social affairs and sustainable corporate governance.
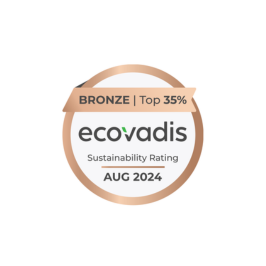
Using valuable water responsibly
Using valuable water responsibly
Water is indispensable for our production processes and safe operations. We set ourselves a target of reducing water withdrawals by 20% compared with the 2019 baseline by 2030 in regions with high or extremely high water stress. By treating wastewater in our own wastewater treatment plants, we can minimize the amount of waste to be disposed of on the one hand and return the treated water to production or discharge it into the public system on the other.
Returning water to the production processes at some sites reduces both the amount of water extracted and the costs. BENTELER tracks and analyzes the quantities of water withdrawn at all sites.
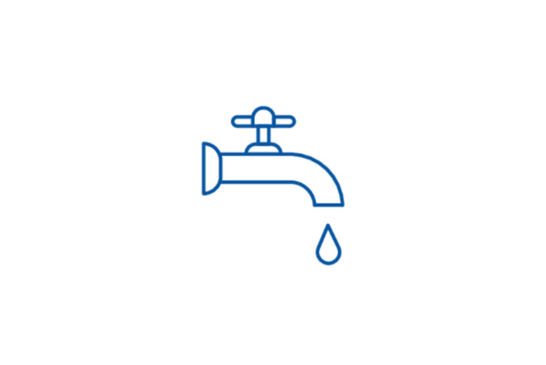
Good for climate and nature:
Preserving biodiversity
Good for climate and nature:
Preserving biodiversity
The conservation and enhancement of biodiversity is essential for intact ecosystems. BENTELER takes biological diversity into account at its locations. We consider designated nature reserves or areas of high biodiversity value to be particularly worthy of conservation and pay particular attention to relevant impacts when implementing activities in these locations.

Circular economy and
recycling of materials
Circular economy and
recycling of materials
Waste avoidance also plays a major role for BENTELER. By recovering and reusing raw materials from waste, for example, we reduce our waste volumes. This helps to conserve resources and also offers cost benefits.
Waste from BENTELER's production activities is continuously recorded at site level, reported monthly and disposed of via certified companies in accordance with local legal requirements.
In 2023, we formulated a group-wide target based on absolute quantities for the first time: By 2030, we plan to reduce the amount of waste in the BENTELER Group by 20% compared to the baseline year, 2019. The formulation of a uniform target for both divisions together with the definition of absolute waste volumes ensures greater transparency within the group.
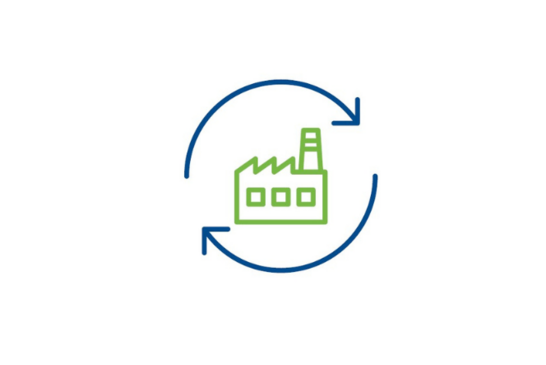
Sustainable products
Sustainable products
We also consider the protection of our environment with our products. If you would like to find out more about which of our products promote sustainability, what expertise we use in this area and how we intend to drive this forward through our research and development activities, you will find further information on the following pages.
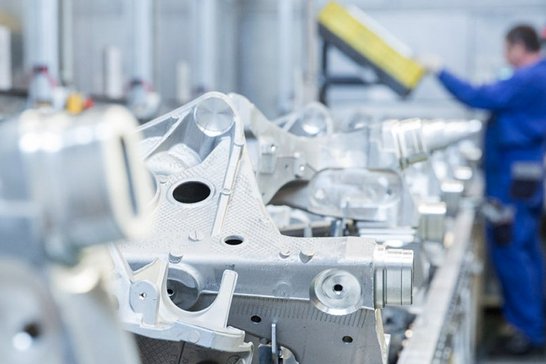